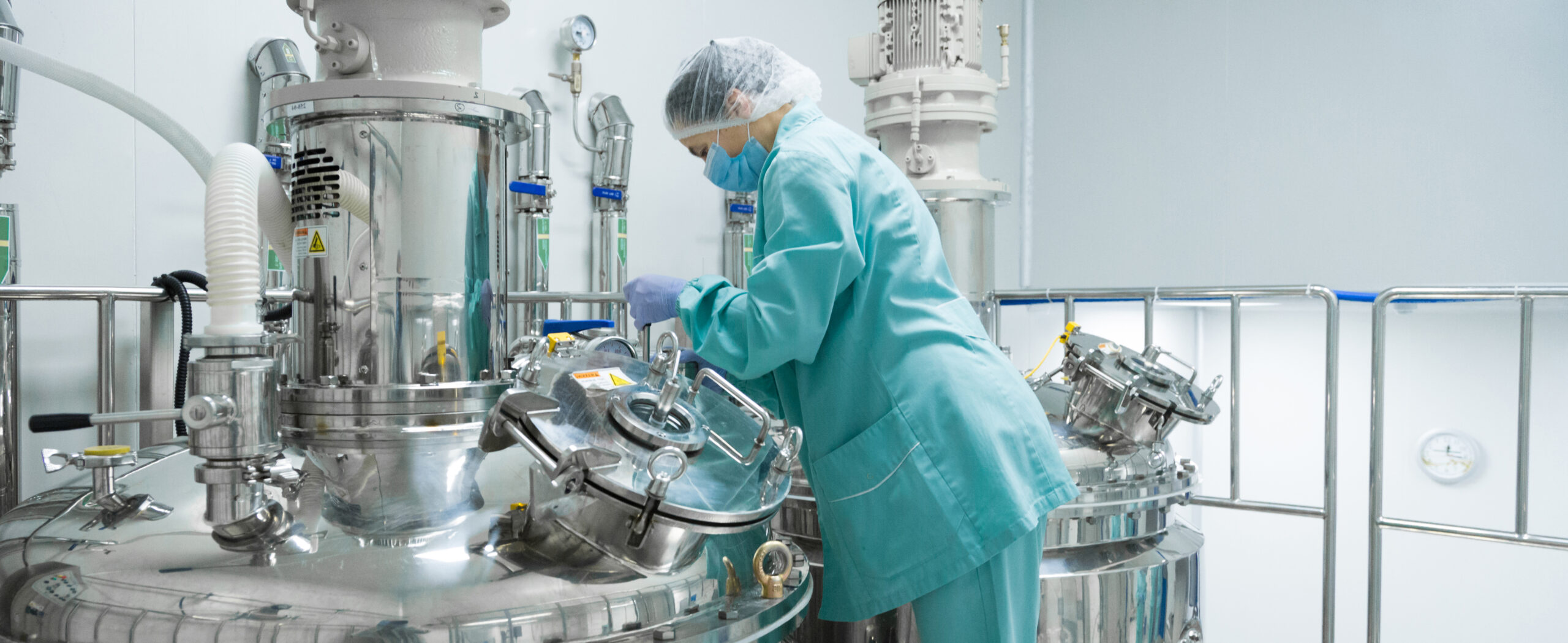
-
September 10, 2024
- 0 Comment
Protecting Sensitive Materials with Effective Tank Blanketing Solutions in Pharmaceuticals
In the pharmaceutical industry, where precision, purity, and safety are paramount, the storage and handling of sensitive materials require meticulous attention. Tank blanketing, a critical process involving the use of inert gases to maintain consistent pressure and prevent contamination in storage tanks, plays a pivotal role in safeguarding pharmaceutical products and ingredients. This article explores the importance of effective tank blanketing solutions, their benefits, and their application in ensuring the integrity of sensitive materials within pharmaceutical manufacturing.
The Role of Tank Blanketing in Pharmaceuticals
Pharmaceutical manufacturing involves storing and processing highly sensitive materials, including active pharmaceutical ingredients (APIs), intermediates, and finished products. These substances are often susceptible to degradation or contamination from exposure to air, moisture, or volatile compounds. Tank blanketing addresses these challenges by creating a controlled atmosphere within storage tanks, thereby mitigating risks and preserving product quality.
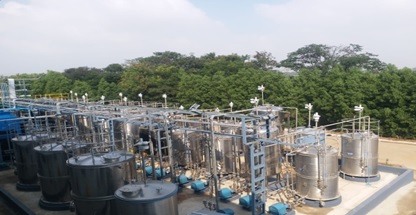
Benefits of Effective Tank Blanketing Solutions
- Inert Gas Protection: Tank blanketing involves the introduction of inert gases such as nitrogen or argon into the headspace of storage tanks. These gases displace oxygen and moisture, creating a non-reactive environment that minimizes oxidation, microbial growth, and chemical degradation of pharmaceutical substances.
- Pressure Control: Maintaining a stable internal pressure is crucial for preventing tank collapse or contamination due to atmospheric exposure. Effective tank blanketing solutions regulate pressure fluctuations within precise limits, ensuring operational safety and reliability.
- Contamination Prevention: By minimizing air ingress and moisture uptake, tank blanketing prevents the introduction of contaminants that could compromise the purity and efficacy of pharmaceutical products. This proactive approach helps adhere to stringent regulatory requirements and quality standards.
Applications in Pharmaceutical Manufacturing
Tank blanketing solutions are integral across various stages of pharmaceutical manufacturing:
- Storage of Raw Materials: Protecting APIs, solvents, and other raw materials from degradation during storage.
- Intermediate Processing: Maintaining inert atmospheres in reactors and processing vessels to preserve chemical reactions and product quality.
- Finished Product Storage: Ensuring the stability and shelf-life of finished pharmaceutical formulations before distribution.
Selecting the Right Tank Blanketing System
Choosing an appropriate tank blanketing system involves considering several factors:
- Gas Selection: Determining the optimal inert gas based on compatibility with stored materials and economic feasibility.
- Flow Control: Implementing precise flow control mechanisms to maintain consistent blanket pressure and minimize gas consumption.
- Monitoring and Control: Integrating advanced monitoring technologies to continuously monitor tank conditions and adjust blanketing parameters as needed.
Regulatory Compliance and Safety Considerations
Compliance with regulatory guidelines, such as those set forth by the FDA (Food and Drug Administration) and international standards (e.g., GMP – Good Manufacturing Practice), is critical in pharmaceutical manufacturing. Effective tank blanketing systems contribute to compliance by ensuring product integrity and safety throughout the storage and processing stages.