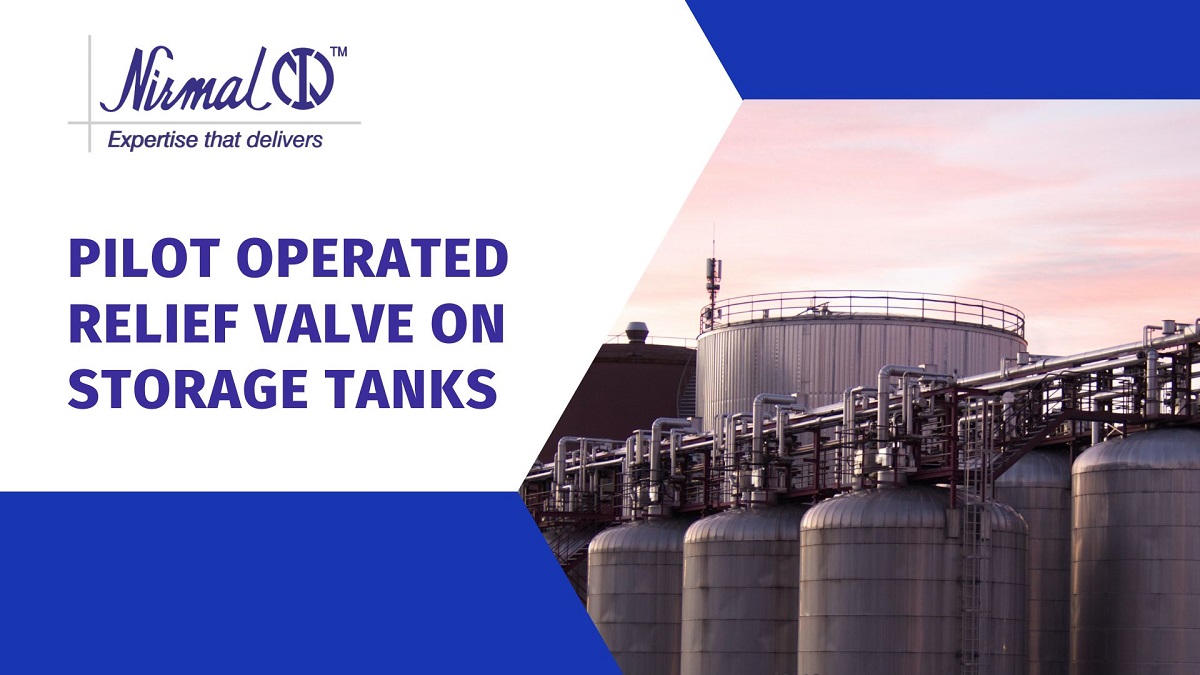
-
September 6, 2022
- 0 Comment
Pilot Operated Relief Valve on Storage Tanks
Pressure and/or vacuum relief valves are used on liquid storage tanks and other process vessels or systems to prevent structural damage caused due to excess internal pressure or vacuum.
Storage tanks are pressurized when liquid is pumped in and compresses the existing vapour or when increasing temperature causes increased evaporation or expansion of existing vapour. Conversely, a vacuum may be created when pumping out or decreasing temperature.
To prevent damage, vapour must be allowed to escape or enter the tank at a specified pressure or vacuum. The volume rate of venting depends upon the tank size, volatility of the contents, the pumping rate, and the temperature. PORV are also called pilot-operated safety valve (POSV), pilot-operated pressure relief valve (POPRV), or pilot-operated safety relief valve (POSRV), depending on the manufacturer and the application.
Pilot-operated relief valves (PORV) are used for emergency relief during overpressure events (e.g., a tank gets too hot, and the expanding fluid increases the pressure to dangerous levels). Pilot Operated Relief Valves serve the same primary purpose as pressure/vacuum relief valves, but with better performance characteristics than weight or spring-loaded valves.
Lower leakage and better flow performance make a pilot operated valve the solution when the focus is product conservation, expanded tank working band, and reduced fugitive emissions. A pilot operated relief valve provides the maximum available leakage control technology as specified in the Clean Air Act of 1990.
The pilot-operated relief valve has two principal advantages over standard types of relief valves:
- it is bubble-tight to set pressure, and
- it is fully open at less than 10% above the set pressure.
Mode of Functioning
The pressure is supplied from the upstream side (the system being protected) to the dome often by a small pilot tube. The downstream side is the pipe or open air where the PORV directs its exhaust. The outlet pipe is typically larger than the inlet. 2 in × 3 in (51 mm × 76 mm), 3 in × 4 in (76 mm × 102 mm), 4 in × 6 in (100 mm × 150 mm), 6 in × 8 in (150 mm × 200 mm), 8 in × 10 in (200 mm × 250 mm) are some common sizes.
The upstream pressure tries to push the piston open but it is opposed by that same pressure because the pressure is routed around to the dome above the piston. The area of the piston on which fluid force is acting is larger in the dome than it is on the upstream side; the result is a larger force on the dome side than the upstream side. This produces a net sealing force.
The pressure from the pilot tube to the dome is routed through the actual control pilot valve. There are many designs, but the control pilot is essentially a conventional PRV with the special job of controlling pressure to the main valve dome. The pressure at which the control pilot relieves is the functional set pressure of the PORV. When the pilot valve reaches set pressure it opens and releases the pressure from the dome. The piston is then free to open, and the main valve exhausts the system fluid. The control pilot opens either to the main valve exhaust pipe or to atmosphere.
Comparison to Conventional Pressure Relief Valves
Advantages
- Smaller package on the larger pipe sizes.
- More options for control.
- Seals more tightly as the system pressure approaches but does not reach set pressure.
- Control pilot can be mounted remotely.
- Some designs allow for changes in orifice size within the main valve.
- Can be used in engines.
- Higher Operating-to-Set Pressure ratio.
Disadvantages
- More complex, resulting in various fail-open failure modes.
- More expensive at smaller sizes (starts to even out as pipe size increases).
- Small parts in pilot valve are sensitive to contaminant particles.
- Soft goods typically installed in pilot valves cannot withstand higher temperature fluids.